"Identifying Hidden Bottlenecks in Supply Chain with Wave Selection and Reading Indicators Analysis"
2024-10-15
Title: Identifying the Hidden Bottlenecks in Your Supply Chain: A Step-by-Step Guide to Wave Selection and Reading
Introduction
As a logistics manager, you're no stranger to the importance of maintaining a smooth supply chain. However, even with the best planning and execution, bottlenecks can still arise at any time. These hidden gems can slow down production, increase lead times, and impact customer satisfaction. In this post, we'll explore the concept of wave selection and reading indicators that will help you identify the first signs of a bottleneck in your supply chain.
Scenario: The Coffee Shop
Let's say you're the manager of a busy coffee shop in downtown Manhattan. You've recently invested in a new espresso machine, which has increased production by 20% but is now experiencing some congestion during peak hours. Your staff is working overtime to keep up with orders, but it's becoming clear that something needs to be done.
Wave Selection: The Problem
Before you can identify the bottleneck, you need to understand your current wave selection process. Most coffee shops use a simple one-size-fits-all approach, where every customer gets their order processed in the same window. However, this might not always be the most efficient way to manage demand. For example:
- A large corporate client is ordering a 500-unit shipment of lattes and cappuccinos.
- A busy Friday afternoon saw a surge in online orders for specialty coffee drinks.
- A new competitor opens across town, attracting a significant amount of customers away from your shop.
Reading Indicators: The Warning Signs
To identify potential bottlenecks before they become major issues, you need to develop a system to monitor your current wave selection and reading indicators. Here are some key signs to watch out for:
- Peak hour congestion: Are there more customers than expected at peak hours? Do you notice a significant increase in orders during this time?
- Order volume spikes: Are orders consistently increasing or decreasing, but not steadily?
- Customer complaints: Are customers reporting issues with delivery times, order accuracy, or overall satisfaction?
- Staff workload and burnout: Is staff working excessively long hours to meet demand? Are they feeling burnt out or stressed about meeting targets?
- Inventory management: Are you running low on key ingredients or supplies? Are your suppliers experiencing difficulties in delivering stock?
Spotting Bottlenecks
Now that you've identified some potential bottlenecks, it's time to start spotting them. Here are some steps to take:
- Conduct a wave analysis: Review your sales data and identify patterns of demand.
- Monitor order volumes and customer behavior: Keep an eye on how customers are behaving during peak hours and when orders increase or decrease.
- Check staff workload and burnout: Are there any signs that staff may be working excessively long hours or feeling stressed about meeting targets?
- Inspect your inventory management: Are you running low on key ingredients or supplies? Are your suppliers experiencing difficulties in delivering stock?
Recognizing Indicators of Changing Bottleneck Flow
As you continue to monitor your wave selection and reading indicators, look out for these signs of changing bottleneck flow:
- Sudden spikes in demand: If demand suddenly increases without any warning, it may indicate a change in customer behavior or supplier availability.
- Staff turnover: If staff members are leaving or arriving at the shop at an accelerated rate, it could be due to issues with workload, burnout, or dissatisfaction with their role.
- Supply chain disruptions: If your suppliers are experiencing difficulties in delivering stock, it may indicate a bottleneck in your supply chain.
Conclusion
Identifying bottlenecks in your supply chain is crucial for maintaining customer satisfaction and driving business growth. By developing a system to monitor wave selection and reading indicators, you can catch potential issues before they become major problems. Remember to conduct regular wave analysis, monitor order volumes and customer behavior, check staff workload and burnout, and inspect your inventory management. If you spot any signs of changing bottleneck flow, take action to address the issue before it becomes a full-blown crisis.
By following these steps and being proactive about managing demand, supply chain disruptions, and staff well-being, you'll be well on your way to creating a smoother, more efficient supply chain that benefits both your customers and your bottom line. Hidden Bottlenecks in Supply Chain: A Step-by-Step Guide to Wave Selection and Reading
Key Indicator | Description |
---|---|
Peak hour congestion | Excessive demand during peak hours (e.g., lunchtime, evenings) |
Order volume spikes | Sudden increase in orders, but not steadily increasing or decreasing |
Customer complaints | Frequent issues with delivery times, order accuracy, or overall satisfaction |
Staff workload and burnout | Excessive long working hours, stress about meeting targets |
Inventory management | Running low on key ingredients or supplies, supplier difficulties in delivering stock |
Spotting Bottlenecks
- Conduct a wave analysis to review sales data and identify patterns of demand.
- Monitor order volumes and customer behavior during peak hours and when orders increase or decrease.
- Check staff workload and burnout levels.
- Inspect inventory management and assess supplier availability.
Recognizing Indicators of Changing Bottleneck Flow
- Sudden spikes in demand without warning.
- Staff turnover (leaving or arriving at the shop at an accelerated rate).
- Supply chain disruptions (difficulty in delivering stock).
Conclusion
Identifying bottlenecks in your supply chain is crucial for maintaining customer satisfaction and driving business growth. By developing a system to monitor wave selection and reading indicators, you can catch potential issues before they become major problems.
Action Item | Description |
---|---|
Conduct regular wave analysis | Monitor sales data and identify patterns of demand. |
Monitor order volumes and customer behavior | Track changes in demand and customer behavior. |
Check staff workload and burnout levels | Assess stress levels among staff members. |
Inspect inventory management | Evaluate supplier availability and stock levels. |
Wave Selection Process
- Identify peak hours (e.g., lunchtime, evenings).
- Determine order volumes and trends.
- Choose a wave selection method (e.g., first-come-first-served, prioritized based on customer behavior).
- Train staff to use the chosen wave selection method.
Reading Indicators for Wave Selection
- Peak hour congestion: More customers than expected during peak hours.
- Order volume spikes: Sudden increase in orders without steady state.
- Customer complaints: Frequent issues with delivery times, order accuracy, or satisfaction.
- Staff workload and burnout: Excessive long working hours or stress about meeting targets.
By following these steps and being proactive about managing demand, supply chain disruptions, and staff well-being, you'll be well on your way to creating a smoother, more efficient supply chain that benefits both customers and your bottom line.
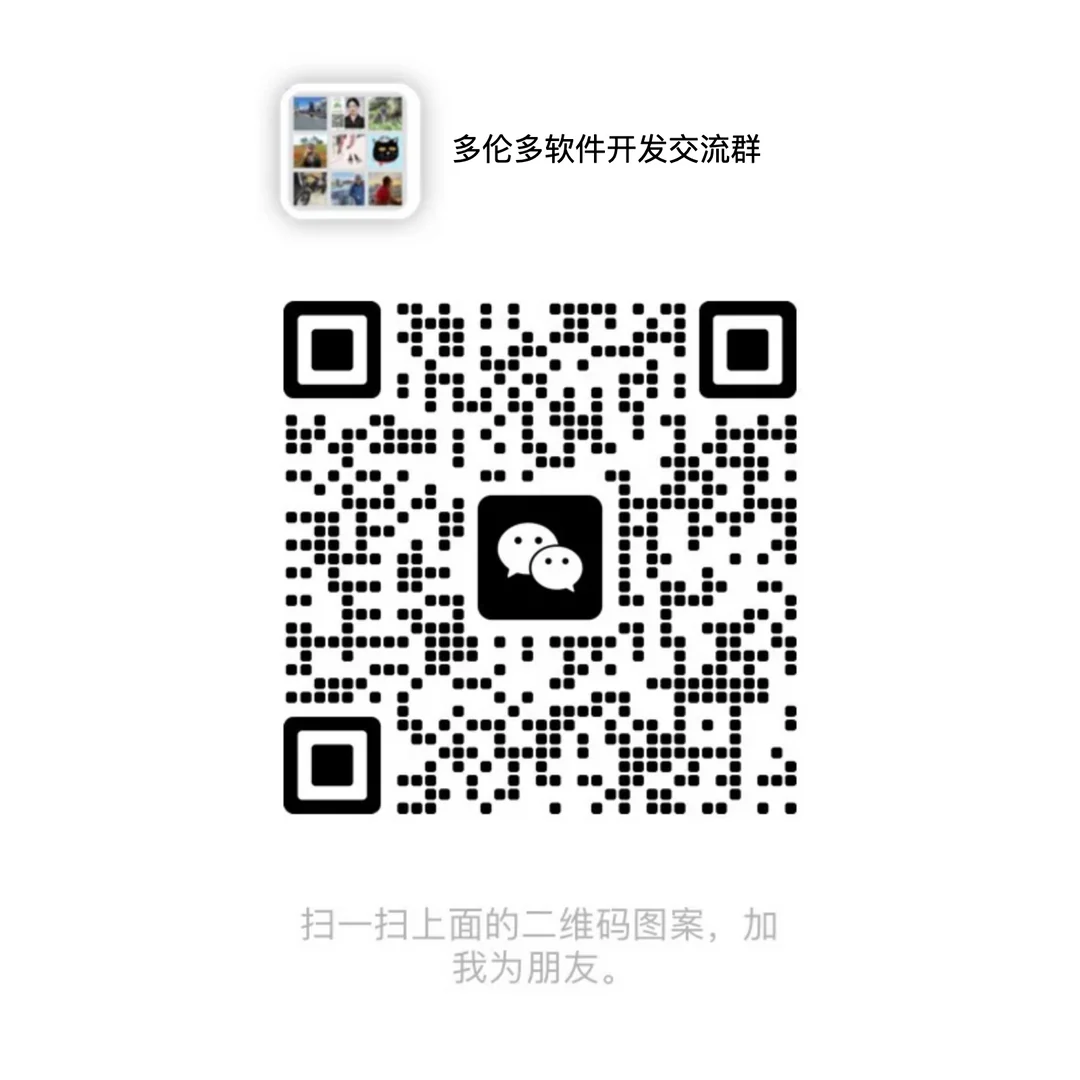