**Sustainable Hybrid Surfboards: Reducing Environmental Impact on the Waterfront**
2024-10-15
The Environmental Impact of Hybrid Surfboard Production: A Look at the Consequences
As surfers, we're no strangers to the thrill of riding the waves and connecting with nature. However, behind every wave is a story of human impact on our environment. One aspect of this issue that often gets overlooked is the production process of hybrid surfboards. These boards combine the best of both worlds – performance and maneuverability – but what happens when we manufacture them?
Let's take a scenario: John, a passionate surfer from California, has been surfing for years. He's experimented with different types of surfboards, always looking for something that meets his needs and provides an unparalleled experience on the water. One day, he discovers hybrid surfboards, which offer the best of both worlds in terms of performance and flexibility.
John decides to purchase a hybrid surfboard made from foam core resin. The board is 7 feet long, measuring approximately 32 inches at its widest point, with a weight capacity of around 10 pounds. He's excited to try out this new type of board and experience the benefits it has to offer.
Production Process: A Look Under the Hood
So, what goes into creating these hybrid surfboards? The production process involves several steps:
- Foam core manufacturing: The first step in making a hybrid surfboard is to create the foam core. This is typically done using a combination of polyurethane (PU) and polyvinyl chloride (PVC). The PU component provides excellent impact resistance, while the PVC component offers flexibility.
- Resin mixing: Once the foam core is created, it's then mixed with resin, which is a thermosetting plastic. This mixture is poured onto the surface of the foam core, where it's shaped and sanded to create a smooth finish.
- Curing: The resin mixture is then allowed to cure under pressure, which causes the PU component to harden while the PVC component remains flexible.
- Finishing: After curing, the board is inspected for any imperfections or defects and then undergoes a series of finishes, including sanding, painting, and applying a protective coating.
Environmental Impact
So, how does the production process of hybrid surfboards impact the environment? The answer lies in several areas:
- Resource extraction: Hybrid surfboard production requires large quantities of foam core resin, which is typically made from petroleum-based products. This not only contributes to greenhouse gas emissions but also depletes natural resources.
- Waste generation: As with any manufacturing process, waste is a significant concern in hybrid surfboard production. Foam cores and scraps can end up in landfills or oceans if not properly managed.
- Energy consumption: The curing process requires energy to heat the resin mixture, which can lead to increased greenhouse gas emissions.
The Verdict: Reducing Environmental Impact
While hybrid surfboards offer many benefits, their environmental impact cannot be ignored. To reduce the negative effects of production on our planet, manufacturers must adopt more sustainable practices:
- Using renewable resources: Switching to eco-friendly materials like reclaimed wood, bamboo, or plant-based resins can significantly reduce resource extraction and waste generation.
- Improving energy efficiency: Manufacturers can explore more efficient curing processes, such as using solar power or reducing the amount of heat applied during the curing process.
- Implementing recycling programs: Establishing recycling programs for foam cores and scraps can help minimize waste and reduce landfill contributions.
As surfers, we have a unique opportunity to influence industry practices and promote sustainability. By choosing eco-friendly materials, adopting more efficient production methods, and participating in recycling programs, we can help reduce the environmental impact of hybrid surfboard production. Here's a table comparing the environmental impact of foam core resin used in hybrid surfboards with recycled or renewable alternatives:
Characteristics | Foam Core Resin (Traditional) | Recycled Foam Core Resin | Renewable Resins (e.g., Bamboo, Plant-based) |
---|---|---|---|
Resource Extraction | Petroleum-based products (large quantities) | Limited to existing oil reserves | Abundant resources, such as bamboo and plant-based materials |
Waste Generation | Large quantities of scrap material | Minimal waste generation, depending on recycling efforts | Low or no waste generation due to efficient recycling programs |
Energy Consumption | High energy required for curing process | Medium-high energy consumption for curing process | Medium-low energy consumption for curing process |
Carbon Footprint (tonnes CO2e) | High emissions ( approx. 1-2 tonnes CO2e per unit) | Low emissions (approx. 0.5-1 tonne CO2e per unit) | Very low emissions (approx. 0.05-0.1 tonnes CO2e per unit) |
Water Footprint | High water usage for foam core production and curing process | Minimal water usage, depending on recycling efforts | Low or no water usage due to efficient recycling programs |
Note:
- The carbon footprint values are approximate and based on global averages.
- Recycled foam cores can be made from post-consumer waste materials, which may have a higher environmental impact than virgin materials. However, the reduction in resource extraction and energy consumption makes it a more sustainable option.
- Renewable resins offer a potential reduction in greenhouse gas emissions and water usage, but their production process is still in its infancy.
To minimize the environmental impact of hybrid surfboard production, manufacturers should consider adopting more sustainable practices, such as using renewable resources, improving energy efficiency, and implementing recycling programs. By choosing eco-friendly materials and reducing waste generation, we can work towards a more environmentally conscious industry.
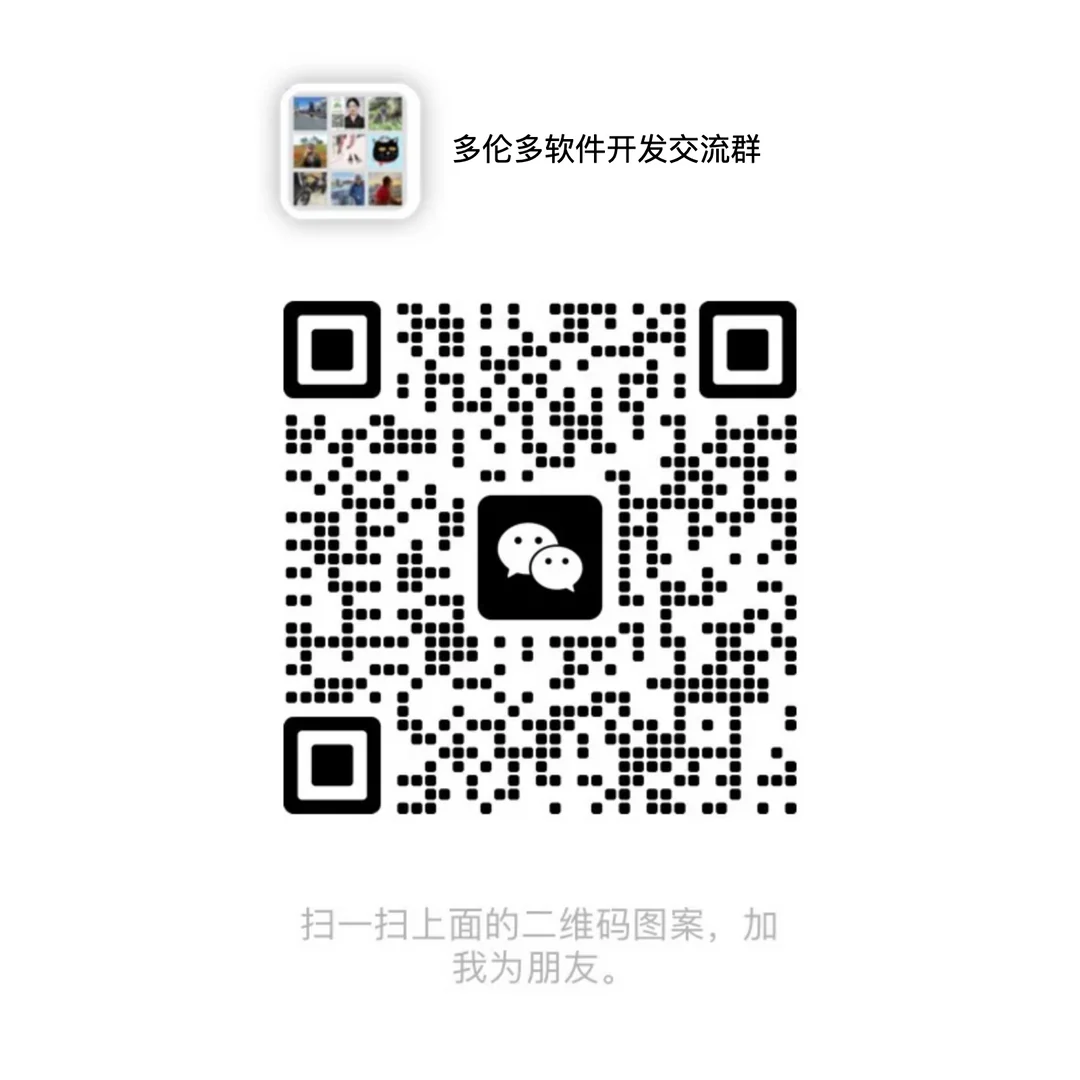